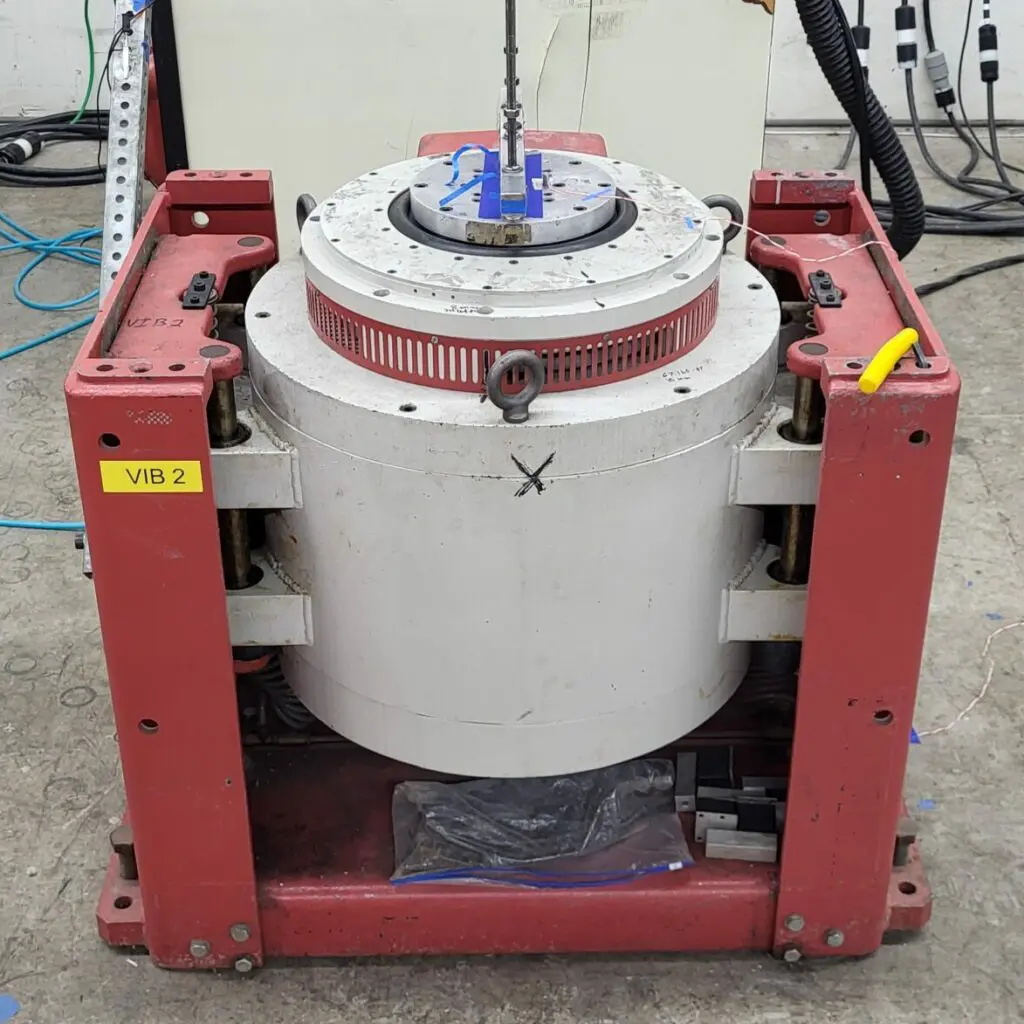
Quest Engineering Solutions is a leading provider of vibration testing and many other testing services.
Vibration testing is the application of mechanical motion to a component, product, system or structure in order to observe its response or degradation over time, and is used to determine how products and components react to vibrational forces during their lifecycle. This type of testing is crucial in assessing the durability and reliability of items that will be subjected to vibrations during transportation, operation, or use in various environments.
Although there is overlap between the two definitions, vibration testing is distinguished from mechanical shock testing in the sense that it is applied for a longer period of time, ranging from a few minutes to many weeks.
Mechanical shock tests have typical durations of less than one second per shock, although multiple shocks over longer time periods are commonly performed.
Electrodynamic Vibration Testing Systems
The vibration input to the test sample is typically applied using an electrodynamic vibration testing system (or “shaker”). The use of this type of general purpose test equipment allows for the application of almost any desired vibration input to the test sample.
The vibration input can be a single sinusoidal frequency, a swept sine, random vibration, sine on random, or a wide variety of other signal shapes. Below is a list of the types of vibration tests that Quest can perform:
Common Types of Vibration Testing
- Sinusoidal Vibration
- Random Vibration
- Sine on Random Vibration
- Random on Random Vibration
- Combined Temperature and Vibration
- Highly Accelerated Lift Testing (HALT)
- Environmental Stress Screening (ESS)
- Shock Response Spectrum (SRS) Analysis
- Modal Analysis
- And more..
The major components of electrodynamic shakers typically consist of a vibration controller, a power amplifier, the electrodynamic shaker itself and the test fixture which is a mechanical adapter between the shaker and the test sample.
The vibration controller is a sophisticated electronic device containing substantial computing power. It can output complex signal shapes and quickly adjust to feedback from an accelerometer located at the vibration input to the test sample. The feedback control loop can be more complex. For example, the vibration amplitude can be controlled to the maximum, minimum or average of multiple accelerometers. Modern vibration controllers can work with hydraulic or electrodynamic shakers with varying specifications, but the limiting factor in the controllers ability to control or even run a vibration profile depends on the physical limitations of the shaker table. These physical limitations include the displacement, force rating, and size of the product being tested relative to the size of the shaker.
We’ve put together a useful calculator tool that allows the user to input the frequency and amplitude values of any random vibration profile in order to determine the overall displacement and acceleration of the profile. This is useful in validating whether a particular random vibration profile can be performed on your electrodynamic or hydraulic shaker. Check out our random vibration calculator by clicking on the link below!
Purpose
The vibration test is generally intended to simulate the expected real-world vibration in typical or worst-case applications. Usually, the test severity is substantially higher than typical real world vibration levels. This is done in order to do a test in hours, days or weeks that simulates years of product life.
This includes tests such as Highly Accelerated Life Tests (HALT) that are much more severe than even the worst-case vibration expected in the real-world.
And there are more modest tests such as Environmental Stress Screening (ESS) which is done to weed out weak units that would fail early in real-world operation, and then ship to customers only those units that demonstrate their hardiness by surviving a test that is sufficiently mild that it does not seriously reduce the product’s expected remaining life.
Although the test amplitude is typically higher than the expected real world amplitude, the shape of the vibration test signal is intended to closely follow the actual signal shape expected.
For example, to simulate the vibration expected for equipment mounted on a wall inside a helicopter, one might test with simultaneous sinusoidal vibration at the frequencies associated with the rotation of the helicopter rotor blades, superimposed on a random vibration covering a wide frequency range associated with how the helicopter structure vibrates due to other vibration sources.
Applications
For most applications, typical test frequencies are between 5 Hz and 3 kHz. An example that often uses lower frequencies is the simulation of the shipping environment. Transportation of a product by truck or air often exposes the packaged product to higher vibration levels than it will see duration operation.
The product packaging, of course, is designed to mitigate or, hopefully, eliminate any damage occurring during shipment. While shipping vibration tests are typically performed using electrodynamic shakers, it is also very common to use a purely mechanical truck ride simulator that looks a lot like the back of a truck.
Vibration tests are usually performed in all 3 axial directions, one axis at a time. Shakers are typically oriented to shake the test sample in the vertical direction, and the test sample is rotated in order to apply vibration in other axial directions.
Small test samples are sometimes mounted to the sides of a cube shaped fixture as a convenient way to apply vibration in different axial directions.
Larger test samples, or those that must remain vertically oriented for functional reasons, are usually vibrated horizontally using a slip table. The typical slip table consists of a massive metal plate (often made of magnesium to help keep the weight down) sitting on an even more massive granite block, with lubricating oil continuously pumped between the plate and the granite block.
The plate must be very level and the friction is so low that the plate can be moved by hand. The test sample is sturdily attached to the top of the plate and the shaker is rotated to a horizontal direction in order to drive the plate and the attached test sample horizontally. Quest’s vibration equipment is highly adaptable and can be customized to meet your special vibration test and vibration analysis requirements. Some of the types of fixturing and equipment that Quest uses include:
Vibration Test Fixturing and Equipment
- Slip Tables
- Head Expanders
- Cube Fixtures
- Load Bearing Platforms
- Custom-made Fixturing
Response accelerometers are sometimes placed at points of interest on the test sample. A vibration response that is substantially higher than the vibration input is called a resonance. A common test plan is to do an initial sine sweep or random vibration test to search for resonances and to then perform sinusoidal vibration tests at the most significant resonance frequencies.
Quest Engineering Solutions provides a broad range of vibration and shock testing services, and is a fully accredited ISO 17025:2017 test laboratory and member of the National Association for Proficiency Testing (NAPT). As a member of NAPT, we regularly conduct vibration and other testing to verify that our test results are accurate and in compliance with strict tolerance limits. We have a variety of vibration test systems of different sizes and broad test capabilities. Our experience can help you choose the tests which will optimize your product’s design and reliability. We can provide vibration test recommendations, or test to international standards, including:
Vibration and Shock Test Standards
- ANSI C136.31
- ASTM D4169 Package Testing Vibration
- EN/IEC 61373
- EN/IEC 60068-2-64
- EN/IEC 60068-2-6
- EN/IEC 60601
- ISO 16750-3
- MIL-STD-1312
- ISTA Package Testing Standards, including ISTA 1, 2, and 3 Series Vibration tests
- MIL Standards, including MIL-STD-810G, MIL-STD-202, MIL-STD-883, MIL-STD-167
- GR-63-CORE
- JEDEC Standards: including JESD22-B103B
- And more..
Quick Links