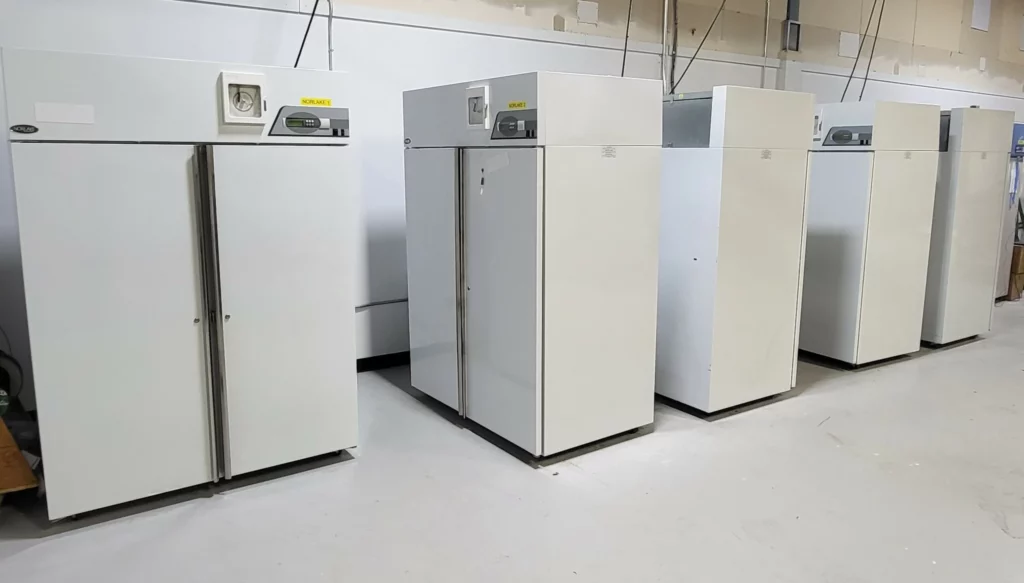
Quest Engineering Solutions is a leading provider of accelerated aging testing and many other testing services.
Accelerated aging testing simulates real time shelf-life aging of transportation packaging, primary packaging, or medical devices in order to validate shelf-life claims. The most common standard for accelerated aging is ASTM F1980. This standard is listed in ISO 11607-1 as being an approved test method for validating materials, packaging, and sterile barrier systems.
Accelerated Aging testing allows the manufacturer to validate shelf-life claims in weeks or months, as opposed to years, and is sometimes performed in conjunction with a real-time aging test or package integrity testing to demonstrate package integrity over the life of the product. The end goal is to provide confidence that the product will meet its expected lifetime and reliability goals without having to wait an entire life cycle to get results.
Accelerated Aging tests are commonly performed to demonstrate that a product can be expected to be stored for a number of years and still function as required. To expedite the effects of time, the product is subjected to temperature and humidity conditions more severe than it would typically experience in its shipping, storage and operational life cycle.
Our 10,000 sq. ft. facility is equipped with dozens of accelerated aging chambers capable of supporting large volumes of test samples at various conditions, including accelerated aging conditioning that requires humidity control.
Check out our ASTM F1980 Accelerated Aging Calculator below to determine the test length, or experiment with different test variables in order to determine the amount of time required at a given temperature to simulate the desired product shelf life.
Acceleration Rate
The Acceleration Rate (also called the Accelerated Aging Rate, Accelerated Aging Factor, or Acceleration Factor) is defined as the ratio of the real-world life-time to the test duration. The higher the acceleration rate, the less reliable the test is. For example, a one year accelerated aging test intended to demonstrate a 10 year storage life (acceleration rate of 10), will be much more valid than a one month test at more extreme conditions that is also intended to demonstrate a 10 year storage life (acceleration rate of 120). There are two reasons for this:
- Using more extreme conditions (for example, higher temperatures) in order to increase the acceleration rate can result in failure modes that would not occur in real-life (for example, melting of plastics).
- The acceleration rate must be determined from theory or previous experiments on similar products, rather than experiments on the actual product, because that would require that the real-time test be performed and thereby take the time that one is trying to avoid by doing an accelerated test. To the extent that the actual product acceleration rate differs from theory or experimental data on other products, the size of the error tends to increase with a higher acceleration factor. For this reason, testing standards and regulatory requirements impose maximum aging rates that can not be exceeded when testing critical products such as medical products that must remain sterile while in storage.
The best understood and experimentally validated acceleration rate, and therefore the one that is most commonly used and accepted, is the Arrhenius Equation which states that each 10°C increase in temperature results in a doubling of the acceleration rate. For example, if the normal product storage temperature is 25°C, the acceleration rate at 35°C will be 2, at 45°C it will be 4 and at 55°C it will be 8.
In conjunction with a package validation test plan (within ISO 11607-1 guidelines), accelerated aging can generate quick results. Accelerated aging data is useful to produce a broad understanding of the effects time may have on a product.
Common Accelerated Aging Test Standards:
- ASTM F1980: Accelerated Aging of Sterile Barrier Systems for Medical Devices
Quick Links