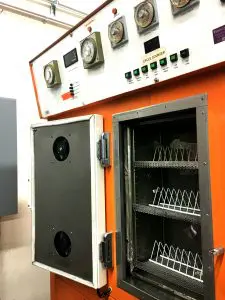
Quest Engineering Solutions is a leading provider of thermal shock testing and many other testing services.
Thermal shock testing assesses how well materials, components, or products can endure rapid temperature fluctuations, simulating real-world stresses they may face, and it can also be used to evaluate a product’s lifespan. This testing identifies weaknesses such as cracking or warping, ensures reliability and durability, predicts product life, and ensures compliance with industry standards. Typically, it involves transferring items between hot and cold chambers to simulate these rapid changes. Thermal shock testing is crucial in various industries, including electronics, automotive, aerospace, consumer appliances, and construction, to ensure components can endure thermal stress. It benefits product design by identifying failure modes, improving performance, increasing customer satisfaction, and reducing the risk of product failures and recalls.
Thermal shock testing differs from thermal or temperature cycling in that it is typically defined as a change in temperature extremes exceeding 15°C per minute. For many specifications, transition from one temperature extreme to another must occur in less than a minute. Testing is typically performed using a thermal shock chamber, an environmental chamber equipped with boost-heat or boost-cooling, or other type of auxiliary heating and cooling system.
A conventional thermal shock chamber consists of separate “hot” and a “cold” compartments. The temperatures of the hot and cold compartments are separately programmed and maintained at their required set points. Test specimens are loaded into the thermal shock chamber and shuttled between the hot and cold compartments in as little as 15 seconds. Once the test specimens transition into the hot or cold compartment, the specimens remain there for the “dwell” period of the profile, of which the duration is based on the total mass of an individual test specimen.
This testing can be performed as part of a screening or qualification, to determine product failure modes, or to be used as a design tool to gather MTBF (Mean time between failure) data in order to determine the mortality rate of a particular test specimen.
Quest Engineering has the capability to perform thermal shock on a wide array of units. Our specially designed Thermal Shock Chambers allow samples to transition between extreme hot and extreme cold conditions. Our chambers are equipped to test in the range of -80°C to 225°C, and can perform cycles for weeks on end without interruption.
High Ramp-Rate Testing
Quest utilizes a standalone forced-air heating and cooling system for testing samples that are too large for Quest’s Thermal shock machines, or for temperature cycling requirements that require faster or slower ramp rates than 15°C per minute. This system allows for the controlled heating and cooling of almost any space, including custom-made test chambers and conventional environmental chambers. This is useful for products of an unusual size or shape, for meeting strict test requirements, boosting existing environmental chamber capability, and for environmental testing combined with other test disciplines; such as temperature and vibration, temperature and shock, and temperature and altitude testing.
Common Thermal Shock Tests:
- MIL-STD-810
- MIL-STD-202
- MIL-STD-883
- JEDEC Standards, including JESD22-A106B
- DEF-STAN 00-35
- IEC 60068
- IPC-TM-650
- ISO 21736
- ASTM C484, and more.
Quick Links