Quest Engineering Solutions is a leading provider of airflow testing, and many other testing services.
Airflow Testing
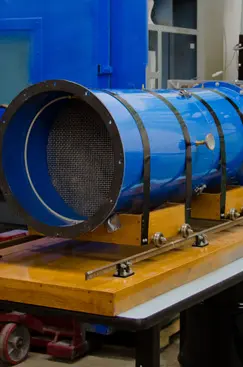
Airflow testing is the measurement of the movement of air through, into, or out of a component or product, or the measurement of the performance characteristics of an air moving device, such as a fan or blower.
Airflow Impedance
The movement of air through a complex electronic product, or through a simple duct, results in the air flow being restricted compared to air flow in free space. The product therefore has an impedance to airflow. This impedance can be measured by forcing air to flow through the product, using a calibrated airflow test chamber, and measuring the pressure difference between the inlet and outlet of the product.
This pressure difference ( typically measured in the USA in units of “inches of water”) increases as the quantity of air (typically measured in the USA in units of cfm, cubic feet per minute) increases. One thereby obtains the product “impedance curve” showing the pressure difference increasing from zero at zero airflow and increasing with increasing cfm. This curve typically increases faster than linearly at low airflow rates and in the typical intended operating range.
Airflow Performance
The airflow performance curve is also measured using a calibrated airflow test chamber. Here we are measuring the performance of an air moving device such as a fan or blower. When the fan is operated in a free field, its airflow performance is high. As the impedance to airflow increases, the amount of airflow decreases. The airflow performance curve is also typically plotted as pressure versus airflow. In the USA this is again typically in units of inches of water versus cfm.
Operating Point
Very similarly to economics, where the price of a product is determined by where the supply and demand curves intersect, the product airflow operating point is determined by where the product impedance curve intersects with the fan performance curve. In a well designed product, this is a stable point not only well within the maximum airflow capability of the fan, but also low enough to minimize unwanted fan noise
Of course, there are more complex situations where the product contains multiple fans and/or the product may have multiple physical configurations (such as the addition of optional circuit boards)
Internal Airflow Measurements
The above discussion refers to external measurements where the product is a “black box” and we are simply testing the total characteristics between the input and output. Internal airflow measurements consist typically of using small air velocity probes to plot how air flows through a product. This is also commonly done via simulation by creating a detailed CAD (computer aided design) model of the product and performing an FEA (finite element analysis).
Airflow testing can help you optimize product cooling, while minimizing product size and noise.
Quest personnel perform airflow tests on prototypes or fully functional products, using our airflow test chamber with a VFRR of 0 to 450 cfm.
Common Airflow Tests
- System Impedance Determination
- Air Mover Characterization (fans and blowers)
- Product Design Optimization for Reliability Enhancement
Common Airflow Measurements
- Air Velocity Measurements
- Airflow Testing at varying air inlet temperatures
- Measurement of component temperatures while varying air velocity and inlet air temperature
- Static Pressure vs CFM Measurements
Quick Links